Located in Chester, Pennsylvania on the Delaware River, the Sun Shipbuilding and Drydock Company built tankers and other ships. Its 70+ years in operation spanned the period when asbestos was used to construct military vessels and ships of all kinds. As a result, the company’s workers and anyone who spent time on its property were exposed to the carcinogenic material and at risk for malignant mesothelioma, asbestosis, lung cancer, and other asbestos-related diseases.
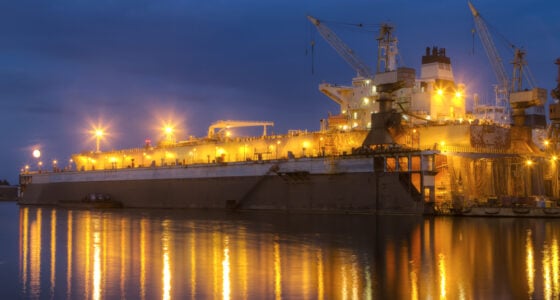
Why Was Asbestos Used in Shipbuilding?
Though today we know that asbestos is a dangerous, highly carcinogenic material, in the 20th century and for centuries before, it was prized for its strength, durability, and insulating abilities. Known for preventing exposure to heat and acting as a flame retardant, it became increasingly popular in the United States around the end of the 19th century, when it was recommended or required by many municipalities and organizations for fire prevention purposes.[1]
These characteristics came to the forefront during World War II, when they were considered crucial for all types of military applications, particularly for shipbuilding. Between 1932 and 1943, the demand for asbestos in the United States grew from 18,198 tons to 783,611 tons,[2] and a significant amount of this was used in Navy ships and other vessels supporting the war effort. The military ordered it applied to pipes, boilers, and engine rooms to protect both service members and equipment and specified the exact amount of the material that was to be used in gaskets, filters, packing, plastic materials, and other components to increase durability and minimize flammability.[1]
A former Navy official testified that World War II destroyers carried 24 to 30 long tons of thermal insulation per ship, and USS Iowa class battleships carried nearly 465 long tons of thermal insulation. Nearly every pipe and ventilation duct on ships commissioned by the military was covered with asbestos insulation.[1] This well-established practice continued until the 1980s when the Environmental Protection Agency confirmed what many had long suspected – that asbestos exposure was linked to malignant mesothelioma and other deadly illnesses.
Did Sun Shipbuilding & Drydock Use Asbestos?
Like other shipbuilders worldwide, Sun Shipbuilding and Drydock relied on asbestos in its shipbuilding process. The inexpensive, readily available material had long been viewed as a miracle mineral for insulating and strengthening the freighters, tankers, and other vessels the company built. Sun Shipbuilding and Drydock also featured a ship repair department that exposed its workers to asbestos put in place by other shipbuilders.
Sun Shipbuilding & Drydock Company took part in the U.S. Maritime Commission’s National Defense Program and followed government specifications in its extensive use of asbestos to insulate boiler rooms and engine spaces. Its heat-resistant properties made it ideal for protecting ships and their crews from fire hazards, and it offered the additional benefit of protecting against corrosion, so the shipyard continued this practice on commercial ships as well. This shipyard built its last ship in 1979 and was sold in 1982 before the impact of asbestos regulations was felt in the shipbuilding industry.
History of Sun Shipbuilding & Drydock
Sun Shipbuilding & Drydock got its start as the Sun Shipbuilding company when the brothers, who were president and vice president of Sun Oil Company, created it in 1916. The Pews established the company on the banks of the Delaware River, on a site that they purchased for $5 million because the company needed tankers to transport crude oil from its fields in Texas to its Marcus Hook, Pennsylvania refinery. Its first vessel, a freighter called the SS Chester Sun, launched on October 30, 1917.[2]
Sun Shipbuilding quickly became a major commercial shipyard, employing over 10,000 people and providing both shipbuilding and repair work for the war effort. By the time World War I had ended, the yard had built three minesweepers and six oil tankers for the Navy and was ready to expand. It added a dry dock, created a ship repair department, and changed its name to Sun Shipbuilding and Dry Dock Company. The nearby Robert Wetherill Engine Works machine shop and foundry were added to the shipbuilding company’s operations to build its diesel engines, and Sun Ship became the sole licensee of the Doxford Diesel Engine, which was the main propulsion for more vessels than any other brand. This made Sun the country’s largest builder of marine diesel engines.[2]
Sun Ship invented the use to replace riveted plates when building pressure vessels, and in 1931, launched the first all-welded ocean-going vessel, marking a new era in shipbuilding. Welding cut building time and costs and increased the strength of the ship. This allowed the U.S. shipbuilding industry to construct three times more ships than would have been possible before the technology was introduced. It also introduced more asbestos into the shipbuilding process, as welding tools make extensive use of the carcinogenic material.[2]
When World War II began, Sun Shipbuilding and Dry Dock Company expanded its shipyard from 8 to 28 shipways to meet the demand imposed by the United States Maritime Commission. The yard focused on oil tanker production and technology and redesigned its previous model to the T-2 tanker that could hold over 141,000 barrels of oil. Sun Ship produced 285 vessels during World War II, accounting for 40 percent of the U.S. oil tanker fleet that furnished 80 percent of the oil and gasoline used during the war. The shipyard built one ship per week during peak production while also playing a vital role in ship repair. The yard repaired over 1,500 vessels damaged by bombs, torpedoes, and mines and, at its peak, employed over 35,000 workers, making it the largest single shipyard in the world. [2]
After World War II, Sun Ship continued to play an important role in shipbuilding, repair, and design. It built the world’s largest hopper dredge for the Army Corps of Engineers and the first supertanker. It developed an Aero/Hydrospace and Industrial Products department that explored non-marine projects, including producing the support anchor components of the Verrazano Narrows Bridge. Its Aerospace division developed the solid propellant rocket motor cases for the Atlas Rocket and the hold-down clamps for the Saturn V rocket. In 1967, it launched the fastest and largest cargo ship built at the time and converted an oil tanker into an ice-breaking tanker that was the first to successfully navigate the Northwest Passage. Sun Shipbuilding also continued its government contract work, including creating a prototype of the Deep Submergence Rescue Vehicle to rescue damaged or sunken submarines.[2]
Sun Shipbuilding and Drydock Company launched its last ship in 1979 and was sold in 1982 to a Texas businessman. The yard was renamed Pennsylvania Shipbuilding but closed in 1989. It was demolished in 2005 and is now the site of a casino and racetrack.[2]
How Did Sun Shipbuilding Drydock Use Asbestos?
Even before the military specified the use of asbestos in shipbuilding, the industry relied on the material to insulate and strengthen the vessels it was building, to ensure tight seals in valves and pipes, and even to protect its workers from the high heat involved in welding parts together.
Materials that would have exposed Sun Shipbuilding and Drydock employees to asbestos include:
- Insulation
- Pipe insulation
- Spray-on insulation
- Boilers
- Cement
- Concrete
- Pipes
- Boiler cladding
- Furnace firebricks
- Floor tiling
- Doors
- Wall panels
- Pumps
- Gaskets
- Valves
- Sealants
- Welding materials
- Packing
- Textiles
- Asbestos Rope
- Safety gloves
- Fireproofing material
- Adhesives
As one of the largest shipyards in the world, Sun Shipbuilding and Drydock employed many different types of skilled laborers. While the yard and drydock were contaminated by asbestos throughout the site, certain employees worked directly with asbestos-containing materials and were at greater risk of breathing in asbestos fibers. These included:
- Welders
- Electricians
- Insulation workers
- Machine operators
- Crane operators
- Repair workers
- Boiler workers
- Demolition or shipbreaking workers
- Longshoremen
- Laborers
- Pipefitters
- Painters
- Ironworkers
- Carpenters
In addition to the dangers faced daily by shipyard workers at Sun Shipbuilding and Drydock, there was a significant risk to their family members and members of the community who were exposed to asbestos dust that workers carried on their hair, skin, and clothing. This secondary asbestos exposure has been responsible for many cases of malignant mesothelioma and other asbestos-related diseases: There have been numerous stories of wives being sickened after years of shaking out asbestos-covered work clothes before laundering them each night, of the children of shipyard workers being sickened after years of sitting on their father’s laps when they returned home from work each day and even of workers in nearby diners being sickened from having served asbestos-dust covered workers when they ate their meals between shifts.
Were You Exposed to Asbestos at Sun Shipbuilding and Drydock?
Though Sun Shipbuilding’s highest production years were those surrounding World War II, the shipyard and repair shop were busy through the mid-1970s when asbestos use in the United States was at its peak. With the latency period for malignant mesothelioma averaging fifty or sixty years after occupational asbestos exposure, there is a good chance that former workers are at significant risk of being diagnosed with an asbestos-related disease in the future. If you or someone you love worked at the shipyard, it’s important to alert your healthcare practitioner of your exposure history so that they can include it in your medical records and respond quickly should symptoms arise. It’s also a good idea for you to learn as much as you can about the various asbestos-related diseases that you may be at risk for.
If you’ve been diagnosed with an asbestos-related disease and need information about the compensation that you’re eligible for, your best resource will be an experienced asbestos attorney. These compassionate professionals have spent years learning about the various asbestos companies that provided Sun Shipbuilding and Drydock with the materials responsible for your illness. They will listen to your story and provide you with information about filing a personal injury lawsuit, about settlements, about how long the process is likely to take and what you can expect, and about the
asbestos trust funds established by asbestos companies that have sought bankruptcy protection.
Deciding to move forward with litigation is a big decision, and it makes sense to want to take time and consult with your family about whether to move forward, but it’s vital that you gather information as quickly as possible. Each state has its own deadline – called a statute of limitations – for filing a claim against asbestos companies, and once the deadline has passed, it will be too late for you to act. A mesothelioma lawyer will tell you how much time you have and answer all of your questions so that you can make a fully informed decision.
References
- Taylor & Francis Online. (September 29, 2011.). Government and Navy knowledge regarding health hazards of asbestos: A state of the science evaluation (1900 to 1970).
Retrieved from: https://www.tandfonline.com/doi/full/10.3109/08958378.2011.643417#d1e128 - Asbestos Surveys. (N.D.) How Did World War II Impact the Use of Asbestos? A Historical Perspective.
Retrieved from: https://asbestos-surveys.org.uk/asbestos/the-history-of-asbestos-use-around-the-world/how-did-world-war-ii-impact-the-use-of-asbestos/ - Pennsylvania Center for the Book. (Fall 2010.). Sun Ship: Vessels of Progress.
Retrieved from: https://pabook.libraries.psu.edu/literary-cultural-heritage-map-pa/feature-articles/sun-ship-vessels-progress
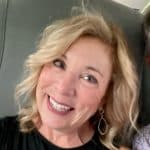
Terri Heimann Oppenheimer
WriterTerri Oppenheimer has been writing about mesothelioma and asbestos topics for over ten years. She has a degree in English from the College of William and Mary. Terri’s experience as the head writer of our Mesothelioma.net news blog gives her a wealth of knowledge which she brings to all Mesothelioma.net articles she authors.
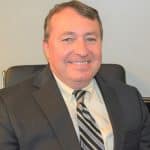
Dave Foster
Page EditorDave has been a mesothelioma Patient Advocate for over 10 years. He consistently attends all major national and international mesothelioma meetings. In doing so, he is able to stay on top of the latest treatments, clinical trials, and research results. He also personally meets with mesothelioma patients and their families and connects them with the best medical specialists and legal representatives available.